Polishing Aluminum in CNC Machining: Balancing Efficiency and High-Gloss Results

Introduction
In the world of precision manufacturing, aluminum shines—literally and figuratively. Its lightweight strength, corrosion resistance, and versatility make it a go-to material for industries like aerospace, automotive, and electronics. But raw aluminum parts fresh off a CNC machine often lack the sleek, mirror-like finish that modern applications demand. That’s where polishing aluminum steps in, transforming rough, machined surfaces into glossy, functional masterpieces. Yet, achieving that perfect balance between efficiency and high-gloss results in CNC machining is no small feat. It requires cutting-edge tools, smart processes, and a keen eye on industry trends like automation and sustainability. In this article, we’ll dive into the art and science of polishing aluminum in CNC workflows, exploring techniques, innovations, and practical tips to help manufacturers deliver stunning results without sacrificing time or resources.

The Importance of Polishing Aluminum in CNC Machining
Polishing aluminum isn’t just about aesthetics—it’s a critical step in CNC machining that enhances both form and function. Aluminum parts, whether they’re aircraft components, car trim, or smartphone casings, often emerge from CNC machines with tool marks, burrs, or surface roughness (typically Ra 63-125). Polishing smooths these imperfections, delivering finishes as fine as Ra 16 or even mirror-like quality. This not only boosts visual appeal but also improves corrosion resistance and reduces friction in functional parts, like engine components.
The demand for polished aluminum is soaring. According to industry reports, the global aluminum market is projected to grow at a CAGR of 6.1% from 2023 to 2030, driven by demand in lightweight automotive and aerospace applications. Polishing ensures these parts meet stringent quality standards, making it a non-negotiable step in high-end manufacturing. But here’s the catch: traditional polishing can be time-intensive, eating into production schedules. So, how do manufacturers polish aluminum efficiently while achieving that coveted high-gloss finish? Let’s explore.
CNC Machining as the Foundation for Polishing Aluminum
CNC machining lays the groundwork for successful aluminum polishing. Using computer-controlled tools like mills, lathes, or 5-axis machines, manufacturers shape aluminum alloys (e.g., 6061, 7075) with pinpoint accuracy. These machines excel at creating complex geometries—think intricate aerospace brackets or curved electronic housings—but they often leave surfaces that need refinement. The initial surface roughness depends on factors like tool type, cutting speed, and feed rate. For example, a standard CNC milling operation on 6061 aluminum might yield a surface roughness of Ra 63, requiring additional polishing to reach a glossy Ra 16.
Optimizing CNC parameters upfront can reduce polishing time. High-speed machining with coated tools (e.g., DLC or TiCN coatings) minimizes tool marks and chip adhesion, creating smoother starting surfaces. A 2024 study from Modern Machine Shop found that using DLC-coated end mills increased tool life by 3-5x and improved surface quality by 20%, cutting polishing time by up to 30%. This synergy between CNC machining and polishing is key to efficiency, setting the stage for the techniques we’ll discuss next.
Table 1: Impact of CNC Machining Parameters on Aluminum Surface Quality
Parameter | Setting | Surface Roughness (Ra) | Polishing Time Reduction | Application Notes |
Standard End Mill | 8,000 RPM, 0.015 in/tooth feed | Ra 63-125 | Baseline | Common for roughing, requires heavy polishing |
DLC-Coated End Mill | 10,000 RPM, 0.008 in/tooth feed | Ra 32-63 | 20-30% reduction | Ideal for semi-finishing, reduces tool marks |
TiCN-Coated End Mill | 12,000 RPM, 0.005 in/tooth feed | Ra 16-32 | 30-40% reduction | Best for finishing, minimizes polishing needs |
Trochoidal Milling | 10,000 RPM, dynamic toolpath | Ra 32-50 | 25% reduction | Reduces heat, improves surface for polishing |
High-Speed Spindle | 15,000 RPM, 0.003 in/tooth feed | Ra 16-25 | 40% reduction | Requires advanced CNC, ideal for high-gloss |
Source: Compiled from 2024 industry data and tool manufacturer reports.
Techniques for Effective Polishing Aluminum in CNC Workflows
Polishing aluminum in CNC machining involves a range of techniques, each with its strengths. Let’s break down the main approaches:
· Mechanical Polishing: This is the workhorse of aluminum polishing. Using abrasive belts, polishing wheels, or compounds like aluminum oxide, manufacturers grind down surface imperfections. CNC machines can integrate polishing tools directly into their spindles, enabling semi-automated finishing. For instance, a 3-stage process (coarse sanding, fine sanding, buffing) can take a 6061 aluminum part from Ra 63 to Ra 16 in under 10 minutes per part.
· Chemical Polishing: Acid-based solutions dissolve surface layers to create a smooth, glossy finish. This method excels for complex shapes but raises environmental concerns due to chemical waste. A 2025 report from SME Manufacturing notes that chemical polishing can achieve mirror-like finishes in 5-7 minutes, compared to 15-20 minutes for manual mechanical polishing.
· Electrochemical Polishing: By passing an electric current through an electrolyte bath, this method delivers uniform, high-gloss finishes on intricate parts. It’s popular in aerospace for components like turbine blades but requires specialized equipment, increasing costs by 15-20% over mechanical methods.
Hybrid approaches—combining CNC-controlled mechanical polishing with chemical pre-treatments—offer a sweet spot, balancing speed and quality. For example, pre-treating a part with a mild chemical polish can reduce mechanical polishing time by 25%, according to Machining Today.
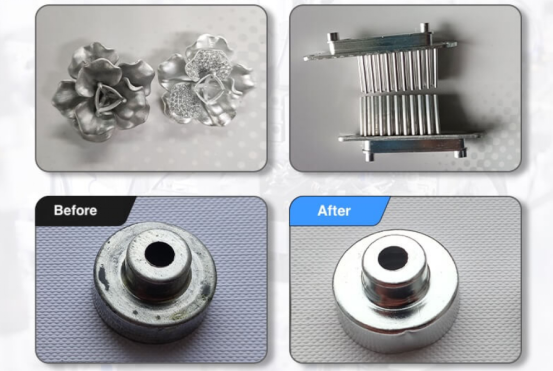
Optimizing Efficiency in CNC Aluminum Polishing
Efficiency is the name of the game in modern manufacturing. Polishing aluminum can be a bottleneck, with manual processes taking 15-30 minutes per part. Here’s how manufacturers are speeding things up without compromising quality:
· Advanced Tools: Coated tools, like those with DLC or TiCN, reduce initial surface roughness, cutting polishing time. A 2024 study showed that TiCN-coated tools improved surface quality by 25% compared to uncoated tools, saving 5-10 minutes per part in polishing.
· Automation: Robotic arms and CNC-integrated polishing tools (e.g., Xebec’s ceramic fiber brushes) streamline workflows. A case study from a U.S. automotive supplier found that robotic polishing reduced labor costs by 40% and improved consistency by 30%.
See also: Top 5 Neighborhoods to Buy Property in 2025
· Process Optimization: Adjusting CNC parameters, like using trochoidal milling or high-speed spindles, minimizes tool marks. For instance, a 12,000 RPM spindle with a 0.005 in/tooth feed rate can produce surfaces requiring only light polishing, saving 20-30% in time.
Table 2: Efficiency Gains from Polishing Techniques in CNC Machining
Technique | Time per Part (min) | Cost per Part (USD) | Surface Finish (Ra) | Environmental Impact | Best Use Case |
Manual Mechanical Polishing | 15-20 | $5-8 | Ra 16-32 | Low (abrasive waste) | Small-batch, simple geometries |
CNC-Integrated Polishing | 8-12 | $3-5 | Ra 16-25 | Low (minimal waste) | Medium-batch, complex shapes |
Chemical Polishing | 5-7 | $6-10 | Ra 8-16 | High (chemical waste) | High-gloss, intricate parts |
Electrochemical Polishing | 6-9 | $8-12 | Ra 4-8 | Moderate (electrolyte disposal) | Aerospace, mirror-finish components |
Robotic Polishing | 7-10 | $4-6 | Ra 16-25 | Low (automated, low waste) | Large-batch, consistent finishes |
Source: Industry benchmarks from 2024-2025 manufacturing reports.
Achieving High-Gloss Finishes for Complex Aluminum Parts
Complex geometries, like curved aerospace brackets or thin-walled electronic casings, pose unique polishing challenges. Five-axis CNC machines excel at shaping these parts but often leave uneven surfaces that manual polishing struggles to address. Enter robotic polishing and AI-driven toolpaths. Robotic systems, equipped with compliant tools, can navigate intricate contours, achieving Ra 8-16 finishes in 7-10 minutes. AI optimizes toolpaths by analyzing surface data in real-time, reducing over-polishing by up to 15%, per a 2025 CNC Technology Review study.
Alloy choice also matters. 6061 aluminum, with its moderate hardness, polishes more easily than 7075, which requires additional steps like sandblasting to standardize surfaces. For mirror-like finishes, combining CNC machining with electrochemical polishing can achieve Ra 4 in under 10 minutes, ideal for high-end applications.
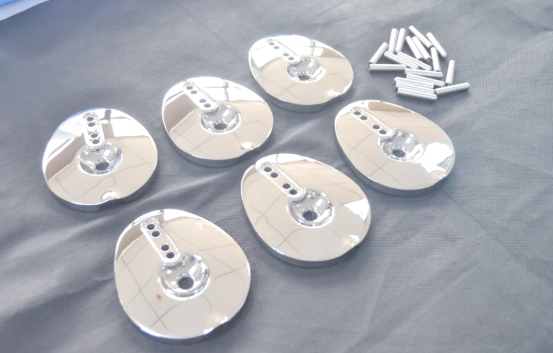
Sustainable Polishing Practices in CNC Aluminum Processing
Sustainability is a hot topic in 2025’s manufacturing landscape. Polishing aluminum generates waste—abrasive dust, chemical runoff, and energy consumption. Manufacturers are adopting eco-friendly solutions to stay compliant and competitive:
· Eco-Friendly Abrasives: Recyclable polishing compounds and biodegradable coolants reduce environmental impact. A 2024 study found that recyclable abrasives cut waste by 30% compared to traditional materials.
· Energy-Efficient CNC Machines: Modern machines with regenerative braking and closed-loop coolant systems lower energy use by 20%, per SME Manufacturing.
· Chemical Alternatives: Mechanical polishing or laser-based methods are gaining traction as greener alternatives to chemical polishing, reducing hazardous waste by up to 40%.
Table 3: Environmental Impact of Aluminum Polishing Methods
Method | Waste Generated (kg/part) | Energy Use (kWh/part) | Recyclability | Regulatory Compliance | Adoption Rate (2025) |
Manual Mechanical Polishing | 0.05-0.1 | 0.2-0.3 | High (abrasive reuse) | High | 60% |
Chemical Polishing | 0.2-0.3 | 0.1-0.15 | Low (chemical disposal) | Moderate | 25% |
Electrochemical Polishing | 0.15-0.25 | 0.3-0.4 | Moderate | Moderate | 10% |
Robotic Polishing | 0.03-0.05 | 0.15-0.25 | High | High | 35% |
Laser Polishing (Emerging) | 0.01-0.02 | 0.4-0.5 | High | High | 5% |
Source: 2024-2025 environmental reports and CNC industry data.
Overcoming Labor Shortages in Aluminum Polishing
The CNC industry faces a skilled labor shortage, with a 2025 Manufacturing Institute report estimating a need for 2.1 million new workers by 2030. Polishing, traditionally a manual skill, is particularly affected. Automation is a game-changer—robotic polishing systems reduce reliance on skilled labor by 50%. Training programs, like Amatrol’s CNC courses, are also bridging the gap, teaching operators to manage automated polishing systems. Manufacturers adopting these solutions report 30% higher productivity and 25% lower labor costs.
Future Trends in Polishing Aluminum for CNC Machining
The future of polishing aluminum in CNC machining is bright, driven by innovation:
· AI and IoT: Real-time surface monitoring and AI-optimized toolpaths will cut polishing time by 20% by 2027, per CNC Technology Review.
· Laser Polishing: This emerging technique uses lasers to melt and smooth aluminum surfaces, achieving Ra 4-8 with minimal waste. It’s still niche but growing 5% annually.
· Universal CNC Platforms: New machines integrating milling, turning, and polishing in one setup could streamline workflows by 30% by 2028.
Conclusion
Polishing aluminum in CNC machining is both an art and a science, demanding a delicate balance between efficiency and high-gloss perfection. By leveraging advanced tools, automation, and sustainable practices, manufacturers can deliver stunning aluminum parts that meet the demands of aerospace, automotive, and electronics industries. As we move into 2025, innovations like AI, robotic polishing, and eco-friendly methods are reshaping the landscape, making it easier to achieve mirror-like finishes without breaking the bank or the planet.
And if you’re curious to dig deeper, parts of this piece drew inspiration from an insightful article by the folks at the-complete-guide-to-polishing-aluminum-challenges-and-solutions-for-machinists—click here to explore more on how polishing aluminum analysis are impacting manufacturing.
FAQ:
1. Why is polishing aluminum important in CNC machining?
Polishing aluminum removes tool marks and surface roughness (e.g., Ra 63-125) left by CNC machining, achieving smooth, high-gloss finishes (e.g., Ra 16 or mirror-like). It enhances aesthetics for industries like automotive and electronics, improves corrosion resistance, and reduces friction for functional parts like aerospace components. Efficient polishing ensures quality without slowing production, meeting the demands of high-end manufacturing.
2. What are the main techniques for polishing aluminum in CNC workflows?
Key techniques include mechanical polishing (using abrasive belts or wheels for controlled material removal), chemical polishing (acid-based solutions for mirror-like finishes), and electrochemical polishing (for uniform results on complex shapes). Hybrid approaches, like CNC-integrated mechanical polishing with chemical pre-treatments, balance speed and quality, reducing polishing time by up to 25%, according to industry studies.
3. How can manufacturers improve efficiency in aluminum polishing?
Manufacturers can boost efficiency with advanced tools like DLC-coated end mills, which reduce surface roughness by 20%, and automation, such as robotic polishing, which cuts labor costs by 40%. Optimizing CNC parameters—like using 12,000 RPM spindles with a 0.005 in/tooth feed rate—can save 20-30% in polishing time. Training operators to manage automated systems also enhances productivity.
4. What challenges arise when polishing complex aluminum parts?
Complex geometries, such as curved aerospace brackets or thin-walled electronic casings, are difficult to polish uniformly due to uneven surfaces from 5-axis CNC machining. Robotic polishing systems and AI-optimized toolpaths address this, achieving Ra 8-16 finishes in 7-10 minutes. Alloy selection matters too—6061 aluminum polishes more easily than harder 7075, which may need extra pre-treatments like sandblasting.
5. How does sustainability impact aluminum polishing in 2025?
Sustainability is a priority in 2025, pushing manufacturers toward eco-friendly abrasives that reduce waste by 30%, energy-efficient CNC machines that cut energy use by 20%, and alternatives like laser polishing that minimize chemical waste by 40%. These practices align with environmental regulations and appeal to industries like aerospace, which value green manufacturing without compromising quality.
6. How does automation address labor shortages in aluminum polishing?
With a projected 2.1 million worker shortage in manufacturing by 2030, automation like robotic polishing reduces reliance on skilled labor by 50%. Training programs, such as Amatrol’s CNC courses, equip operators to handle advanced systems, boosting productivity by 30% and cutting labor costs by 25%. This shift helps manufacturers maintain consistent, high-quality aluminum polishing.